Which Baffles Should You Choose for Shell & Tube Heat Exchangers?
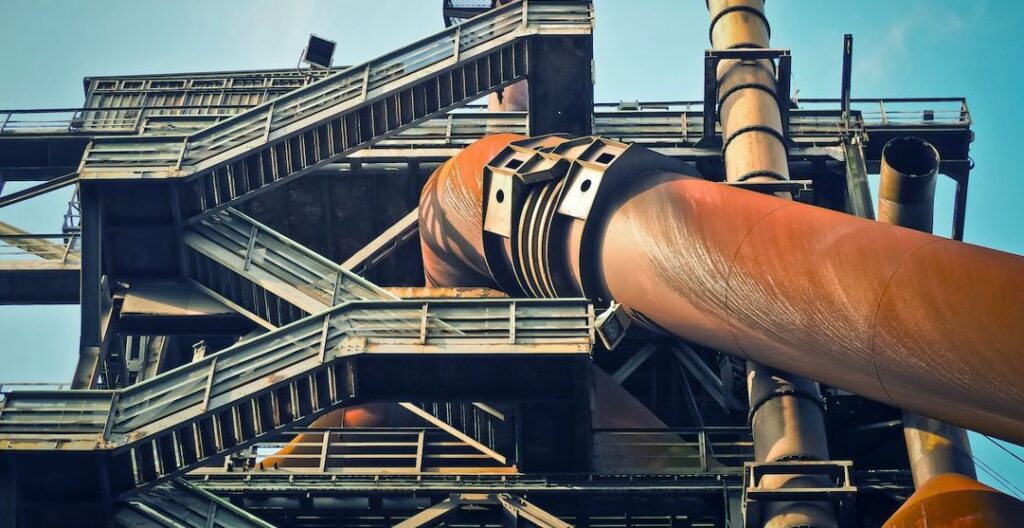
Baffles play a vital role in supporting the tube bundle. They help regulate shell-side fluid flow and improve heat transfer between the two processes. It’s an important structural feature that a shell-and-tube heat exchanger needs to possess. So, which baffles should you choose for your shell-and-tube heat exchangers? Will you opt for the positioning of the baffles to be horizontal or vertical?
What are baffles?
They refer to flow directing or obstructing panels utilised to direct the flow of liquids or gasses, commonly used in some industrial processes such as shell-and-tube heat exchangers, chemical tractors, household stoves and static mixers. These panels are a vital part of the shell-and-tube heat exchanger design. The main function of baffles is to hold tube bundles and direct the flow of fluids for maximum efficiency. These panels are positioned in two ways in shell-and-tube exchangers, either horizontally or vertically.
Horizontal Baffles
Baffles in this position are best for operations where a single-phase fluid is on the shell side. It’s because it helps prevent deposits from building up on the bottom of the exchanger. Also, it prevents stratification allowing warmer fluids in the upper region of the exchanger to mix with the cold fluid below. As a result, baffles in heat exchangers can often provide a higher heat transfer rate.
Horizontal baffles are the primary designs with many shells and tube heat exchangers. These baffles have a significant effect on pressure drop and heat transfer rate. When these heat exchangers have no leakage, the horizontal baffles offer great benefits regardless of shell side fluid.
Heat exchanger manufacturing companies say exchangers with these baffles provide high heat transfer. With this design, the average space between the inlet and outlet valves and first and last baffles is longer than in exchangers with vertical baffles. Therefore, the amount of shell-side fluid flowing along the baffle is greater. It contributes to an increase in flow between the tubes and baffles.
If the shell side fluid flows at a lower velocity, horizontal baffles help keep the process flowing regularly. However, one drawback is these baffles increase the time fluid remains in the shell, which can negatively affect heat transfer.
Vertical Baffles
These baffles simplify the production of two pass exchangers, for example, the F-type shell. This design is suitable for applications where condensation occurs on the shell side. The vertical positioning allows the condensate to flow downward toward the outlet instead of being trapped by the baffle.
Manufacturing companies found that tube and shell heat exchangers with leakage perform best with vertical baffles. The benefit is significant when the shell side fluid is gaseous due to gas’ higher dissipation than liquids. These baffles function best when a lower pressure drop is desired.
The pressure drop experienced in leaking heat exchangers with horizontal baffles is higher than in leaking exchangers with vertical baffles. Therefore, vertical baffles are the best if you are looking for shell-and-tube exchangers to lower pressure drop. The positioning of baffles in a shell-and-tube heat exchanger impacts heat transfer rate and pressure drop. However, the most beneficial baffle positioning depends on the following:
● The application of the heat exchanger
● Characteristics of the processes used for and desired outcomes.
Different processes require varying designs. But a custom shell-and-tube heat exchanger offers the best results for a specific operation.
What’s the main role of baffles?
The main function of baffles in a shell-and-tube heat exchanger is to:
● Support tubes are in place to prevent sagging in both production and operation.
● Stop the outcomes of steam starvation which is stepped up with both fluid velocity and the length of the exchanger.
● Direct shell side fluid flows along the tube field to increase fluid velocity and effective heat transfer coefficient of the exchanger.
Baffle installation
As mentioned, the baffles help support and direct fluids in heat exchangers. Due to this, they need to be well-spaced during installation for optimal performance. The minimum recommendation of baffle spacing is greater than 50.8 mm or one-fifth of the inner shell diameter. However, sections with no tube in the window design affect the recommended spacing within the design. When installing baffles, the main design consideration is that there will be no formation of recirculation zones or slow spots. These two are counterproductive to effectual heat transfer.
Baffles play a vital role in shell-and-tube heat exchangers. Therefore, it’s important to position the baffle according to the type of processes it will perform. Also, ensure that they strictly follow the recommended spacing guidelines for maximum performance. Finally, if you need it for specific functions, you can have it customised depending on the type of process. Considering all these will ensure you get a baffle that perfectly suits your purpose.